Aerosol products have four main components, aerosol cans, valves, material, and ejector gas. Due to the differentiation of product formulations, we often need to consider the corrosiveness and pressure resistance between the filled material and the container when choosing the package. We know that there is a water-based aerosol product, which is highly corrosive to the can. So filling water-based aerosol products the key issue is the corrosion of the can, and the quality of the aerosol can directly affect the corrosion resistance. Factors affecting the quality of aerosol cans, from raw materials, can-making equipment and processes to quality testing, there are many, the following brief introduction.
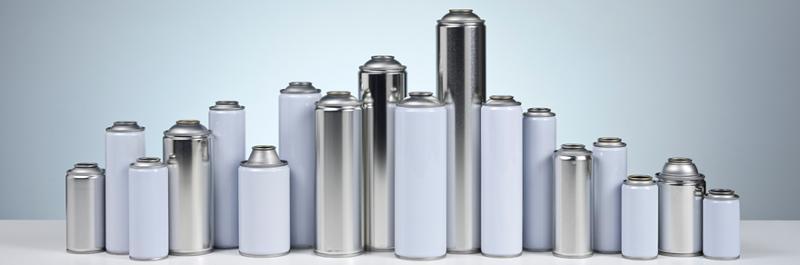
1.The quality of tinplate itself
Tinplate base material used in the manufacture of cans requires high purity, such as impurity content is too high, affecting the ductility, brittleness, hardness and other processing properties and corrosion resistance, at present, most of China's tinplate base material imported from abroad. Some manufacturers in order to reduce costs, the use of low-quality thin tinplate cans, tinplate itself has tiny holes in the sand, resulting in leakage of the cans, the selection should pay special attention to.
2. Can body welding and coating quality
For Aerosol Tin Cans, one of the weaker links is the weld, in addition to the strict requirements of mechanical properties, the weld is easily corroded due to the destruction of the tin layer, and thus the filler coating is a three-piece cans of a key technology, a lot of water-based products leakage cans are due to the filler coating and the contents of the incompatibility caused by. In addition, the current is unstable or unstable quality of copper wire, etc., are easy to product welding, the formation of leakage points.
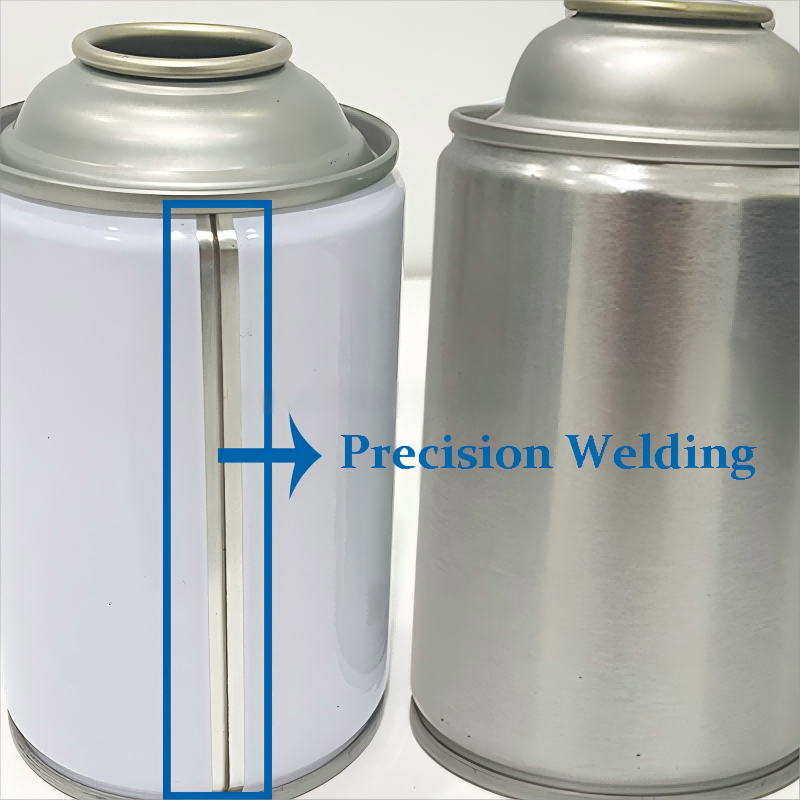
3.The type of internal coating and densification
Internal coating is one of the effective anti-corrosion method of water-based products (except DME as a propellant), but the quality of the internal coating material itself and the coating process will affect the corrosion resistance of the product, such as the coating of some of the naked eye is not easy to find bubbles, the electrochemical reaction is particularly strong in these places, over time it is easy to corrosion and rust so that wear cans, especially in the top and bottom of the lid and the weld contact with the tank body in the cans are prone to produce damage! In addition, the denseness of the coating is more important, many water-based products leakage of cans are present in this place. Currently used in the internal coating of epoxy a phenolic, imide an epoxy, PVC and other types, the use of more epoxy a phenolic, but the quality of different manufacturers are different, the selection should be good compatibility test.
4.Sealing quality
Good sealing equipment and process is an effective guarantee of the sealing performance of aerosol cans, volume sealing of the hook and loop is an important indicator of the test, if the control is not good (including production processes and testing), it is easy to seal the imperceptible micro-leakage.
5.Leak detectio
Aerosol products are mostly flammable and explosive products, each factory aerosol cans must be tested by the online pressure leakage detection machine, while the deformation pressure and burst pressure must be carried out in accordance with the provisions of the sampling to ensure the safety of the product production, storage, transport, use. Some manufacturers in order to reduce costs, not in accordance with the provisions of the leak detection, these cans are very likely to exist in the quality or safety hazards.
6. Sealant
Aerosol cans and cans between the lid by the sealant in order to achieve the sealing requirements, the choice of a good sealant and coating process is critical to the quality of the can, in addition to the quality of the sealant itself should be strictly controlled, the sealant on a variety of solvents, especially strong solvents, DME and other solvency, dissolution, dissolution of the performance of the strict, long time to carry out the test, otherwise it will appear to destroy the sealant and leakage, there have been some of the can factory to appear such a situation. This situation has occurred in some can factories. When applying glue, the broken glue or uneven distribution, blistering, insufficient amount of glue applied, etc. are prone to problems. Due to the aerosol contents are very different, plus the sealing performance can not be determined within a short period of time, the quality of the sealant can only be guaranteed through the long time production experience of the can manufacturer and strict quality control.
From the above points we can know, regardless of the production of which aerosol products, the choice of packaging containers is very important, we not only need to consider the corrosiveness of the contents, but also need to consider the pressure resistance of the can, because the aerosol products belong to the pressure of the product, the filling pressure will be too big burst cans, the pressure is too small may not be able to achieve the desired effect of the spray. Therefore, we need a reasonable combination of product characteristics to choose the right aerosol cans!